Table of Contents
As consumers become more discerning and regulatory standards tighten, manufacturers are constantly seeking innovative ways to enhance their packaging processes. One such innovation is the use of nitrogen generators, which play a crucial role in improving the quality of plastic packaging.
The incorporation of nitrogen gas into the packaging process has proven to be highly beneficial. Nitrogen, an inert gas, helps in various stages of packaging, from production to storage. By utilizing a nitrogen generator for packaging, manufacturers can ensure that the plastic packaging is not only durable but also maintains the freshness and integrity of the products it encases.
Benefits in Plastic Packaging
1. Enhanced Product Shelf Life
One of the primary advantages of using in plastic packaging is the significant extension of product shelf life. Oxygen is a major contributor to the degradation of many products, leading to spoilage and reduced shelf life. Nitrogen, being an inert gas, displaces oxygen within the packaging, thereby slowing down the oxidation process. This is particularly important for food products, where freshness and quality are critical.
2. Improved Package Integrity
Nitrogen generators help maintain the structural integrity of plastic packaging. By filling the headspace with nitrogen, the packaging becomes more resistant to collapse and punctures. This ensures that the products inside are well-protected during transportation and storage, reducing the likelihood of damage and waste.
3. Preservation of Product Quality
For many products, exposure to oxygen can lead to undesirable changes in color, flavor, and texture. Nitrogen generators eliminate this risk by creating an oxygen-free environment within the packaging. This preservation of quality is essential for food items, pharmaceuticals, and other sensitive products, ensuring they remain in optimal condition until they reach the consumer.
4. Cost-Effectiveness
Implementing can be a cost-effective solution for manufacturers. By extending shelf life and reducing waste, companies can save on costs associated with product returns and spoilage. Additionally, nitrogen is a readily available gas, making it an economical choice for large-scale packaging operations.
Applications in Various Industries
1. Food and Beverage Industry
In the food and beverage sector, maintaining the freshness and safety of products is paramount. Nitrogen generators are widely used to package snacks, dairy products, and beverages. The inert gas prevents oxidation and microbial growth, ensuring that the products retain their quality over extended periods.
2. Pharmaceutical Industry
Pharmaceutical products often require stringent packaging standards to maintain their efficacy. Nitrogen generators provide an ideal solution by creating a controlled environment that protects sensitive medications from oxygen and moisture. This ensures that the drugs remain effective throughout their shelf life.
3. Electronics Industry
The electronics industry also benefits from the use of nitrogen generators. Electronic components are highly sensitive to moisture and oxygen, which can cause corrosion and malfunction. Packaging these components helps preserve their integrity and functionality.
Operational Efficiency and Environmental Impact
1. Automation and Control
Modern nitrogen generators come equipped with advanced automation and control systems. These systems allow manufacturers to precisely control the flow and concentration of nitrogen, ensuring consistent quality across all packaging lines. This level of control not only enhances product quality but also improves operational efficiency.
2. Reduced Environmental Footprint
Using nitrogen generators in packaging processes can contribute to a reduced environmental footprint. By extending the shelf life of products, manufacturers can minimize waste and reduce the frequency of product disposal. Additionally, nitrogen is a non-toxic, environmentally friendly gas, making it a sustainable choice for packaging applications.
Choosing the Right Model
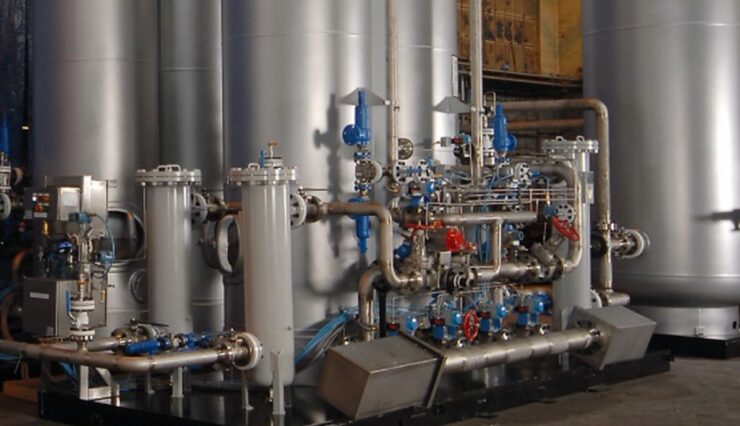
When selecting a nitrogen generator for packaging, several factors need to be considered:
1. Capacity and Flow Rate
The capacity and flow rate of the nitrogen generator should align with the specific needs of the packaging operation. Manufacturers must assess their production volume and choose a generator that can consistently supply the required amount of nitrogen.
2. Purity Levels
Different applications may require varying levels of nitrogen purity. For instance, food packaging may necessitate higher purity levels to ensure product safety and quality. It is crucial to select a nitrogen generator that can deliver the appropriate purity levels for the intended application.
3. Maintenance and Support
Regular maintenance is essential to ensure the longevity and efficiency of nitrogen generators. Manufacturers should choose generators from reputable suppliers that offer comprehensive support and maintenance services. This will help in maintaining optimal performance and minimizing downtime.
Case Studies: Success Stories
1. Snack Food Manufacturer
A leading snack food manufacturer implemented nitrogen generators to improve the shelf life of their products. By replacing oxygen with nitrogen in their packaging, they observed a significant reduction in spoilage rates and an increase in product freshness. This not only enhanced customer satisfaction but also resulted in substantial cost savings.
2. Pharmaceutical Company
A pharmaceutical company faced challenges in maintaining the stability of their sensitive medications. By integrating nitrogen generators into their packaging process, they created a controlled environment that protected the medications from oxygen and moisture. This led to improved product stability and extended shelf life.
3. Electronics Manufacturer
An electronics manufacturer experienced issues with corrosion in their packaged components. By utilizing nitrogen generators, they were able to create an oxygen-free packaging environment, effectively preventing corrosion and ensuring the reliability of their products.
Future Trends and Innovations
Integration with Smart Packaging
The future of nitrogen generators in packaging lies in their integration with smart packaging technologies. Smart packaging, equipped with sensors and IoT devices, can monitor the internal environment of the package in real time.
Advances in Generator Technology
Ongoing advancements are expected to enhance their efficiency and performance. Innovations such as energy-efficient designs and improved automation systems will make nitrogen generators even more cost-effective and environmentally friendly.
Conclusion
The use in plastic packaging offers numerous benefits, from extending product shelf life to improving package integrity. By creating an oxygen-free environment, nitrogen helps preserve the quality and freshness of various products, making it an invaluable tool for manufacturers across different industries. As technology continues to evolve, the integration of nitrogen generators with smart packaging solutions and sustainable practices will further enhance their impact, ensuring that plastic packaging meets the highest standards of quality and safety.